By: Chett Norton, C.E.T & Alison Brent
Thursday, September 10, 2015
In the gasket industry there are a multitude of tests performed on materials that will supposedly help the end user make an educated decision on which material to use based on specific application criteria. However due to the lack of gasket property knowledge, what often ends up happening is that the end user becomes more confused, running the risk of choosing an incorrect material and causing untimely leaks or even unsafe gasket blowouts.
This article is intended to shed some light on four commonly misinterpreted and misunderstood gasket material tests: Flexibility (ASTM F147); Tensile Strength (ASTM D4745, ASTM F152); Sealability (ASTM F2378); and Maximum Pressure.
ASTM F147 – Standard Test Method for Flexibility of Non-Metallic Gasket Materials
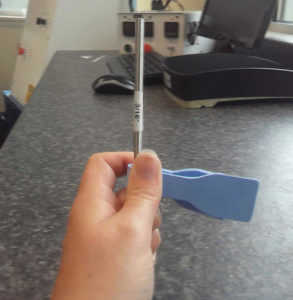
This test method measures the gasket material’s Flexibility both transverse and longitudinal to the grain orientation. This test can also determine quality of the gasket material by determining the product’s Flexibility factor.
In this test, several “dog bone” shaped samples (based on the ASTM F147 standard) are cut in both transverse and longitudinal orientations. These samples are are placed in a conditioning oven at 100˚C (212˚F) for an hour then cooled to room temperature in a desiccator. The test material’s thickness is determined with a micrometer and recorded. The test material is firmly held at one point on a circular mandrel (ranging in diameter from 4.8mm to 101.6mm, starting with the largest diameter) and forced slowly to contact 180˚ of the full diameter. This procedure is repeated using decreasing mandrel diameters on a new sample until a failure occurs. A failure is considered to be any cracks, breaks, or surface separations at the end of the Flexibility test. When a failure occurs the mandrel diameter is recorded.
A Flexibility factor can be calculated by taking the Minimum Diameter divided by the Original Thickness. It is important to understand that when looking at the Flexibility factor the lowest possible value is considered a positive result. For example, Flexibility values are a lot like golf scores, meaning the lower the score, the better. Therefore, with Flexibility a value of 4 would be more flexible than a value of 10.
Tensile Strength (ASTM D4745 & ASTM F152)
At Triangle Fluid Controls we do 2 different types of Tensile testing using ASTM D4745 and F152 meaning we test both little “dog bones” and big “dog bones”. The test used is dependent on the type of material being tested, i.e. fiber, PTFE, and graphite. These “dog bones” are predetermined test specific shaped samples. Tensile testing is a quality control test by measuring the strength of the product, which in turn, determines the conformance of the manufacturing process. It should be noted that Tensile strength is not equivalent to the maximum pressure rating of the product, but more of a standard internal QA check.
ASTM D4745 – Standard Classification System and Basis for Specification for Filled PTFE Molding and Extrusion Materials
The ASTM D4745 Tensile test involves cutting material both transversely and longitudinally (conditioned based on sample type). These samples are then placed and clamped into our Tensile machine with an extensometer also attached to the sample. An extensometer is used to determine the strain measurement of the material under stress. The machine is then set up and parameters of the sample are imported. The machine is then started and runs until a failure occurs (any cracks, breaks, or surface separations at the end of the test). The results are recorded in psi and percent elongation.
ASTM F152 – Standard Test Methods for Tension Testing of Nonmetallic Gasket Materials
The ASTM F152 Tensile test is similar to the D4745 Tensile test except this test only involves samples to be cut transversely (conditioned based on sample type) and no extensometer is attached. These samples are then placed and clamped into the Tensile machine and the test is performed.
ASTM F2378 – Standard Test Method for Sealability of Sheet, Composite, and Solid Form-in-Place Gasket Materials
This test method is suitable for evaluating the leakage rate, sealing properties and characteristics of gasket materials under a load pressure at room temperature (21-30˚C/70-86˚F).
This testing process involves placing a cut sample (conditioned-based on sample type) using the ASTM F2378 specified die dimensions in between 2 flat steel platens. A seating load of 4,640 psi is applied and nitrogen is introduced into the center gasket cavity at a pressure of 580 psi. A timer is set for one hour, forty-five minutes. The evaluation stage occurs next as a manometer is connected to measure any leakage coming through or around the gasket. The leak rate is recorded at one minute, and again at fifteen minutes. The results are recoded and the average leak rate is calculated. The lower the average leak rate, the higher the gasket’s ability to seal. However there are many units used to measure Sealability (mL/min, cc/min or mL/hr) so you must make sure that you are comparing the correct test method and the reported units as well. Sealability is one of the most important characteristics in today’s sealing world, as even “small” leaks are frowned upon due to worker safety and environmental concerns.
Maximum Pressure
Maximum Pressure is used to determine a value where the material can be used safely (at room temperature). The material samples are pressurized until the gasket “blows” out and then using a FOS (Factor of Safety) a number can be determined, however it should be noted that in most cases, gasket materials are not used at room temperature. What we mean by this is that as gasket material is exposed to elevated temperatures the properties of the gasket change, so it is very important to check a PxT (Pressure x Temperature) chart for the material selected and your specific application (pressure, temperature, and media).
For instance, Durlon 9000 is rated for 1500psi, however as you can see in the below PxT chart at 400°F the maximum pressure would be 1000 psi. The Green area = safe to use; Yellow area = Do not use in these conditions or contact TFC applications engineering.
Final Thoughts
Hopefully this gives you a little more understanding and information on these four commonly misinterpreted and misunderstood gasket material tests, so that you can select a quality gasket material or at least be able to compare gasket materials on an “apples to apples” basis. If you are still unsure about gasket material selection, you can download our handy iGasket App, visit our website at www.trianglefluid.com or contact TFC application engineering (tech@trianglefluid.com). Chett Norton can also be reached via Twitter at @TFCgasketguru.